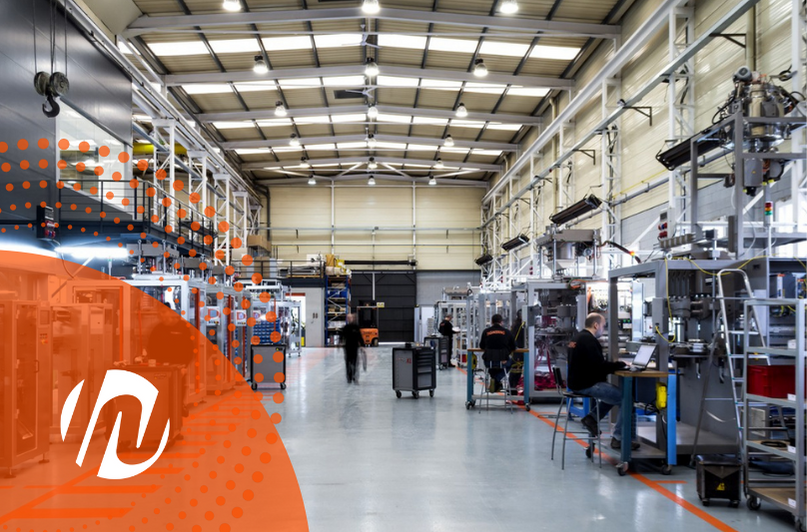
For everyone, the past year 2020 and part of this 2021 hasn’t been easy. The uncertainty, the change of paradigm and the subsequent problems in raw materials, brought changes in companies operation and decision making in some areas.
In the case of INVpack, as a vertical packaging machinery manufacturer, despite the circumstances, the company decided to face the situation as an opportunity to offer a better product, better service and faster delivery.
To achieve it, it was decided to stock the components that make up our single-dose flexible packaging machinery, for sachet and stick pack models.
At the beginning of the pandemic, the purchasing department made an analysis of the purchasing trends so far, and what forecast we could make to optimize all the material and its rotation.
For this reason, in addition to increasing the purchase volume, it was decided to outsource the standard groups that make up the machinery and thus in turn offer greater reliability thanks to the verification of each of them.
To this end, the company's direction thought that was absolutely necessary to hire a new professional in the team, who was incorporated as soon as possible to be able to work on these extra tasks to the usual work of the purchasing department.
The pandemic caused also problems related with raw materials, which has generated a considerable increase in the prices of the materials used to manufacture the machinery. This has also led to an increase in transportation costs worldwide.
As a result of all these problems, 90% of the suppliers passed it on with an increase in their prices.
For the purchasing department, this situation has generated an added problem to their daily tasks, which they carry out in the most professional way possible without affecting the quality of the machines.
At the same time, the company decided to improve processes and make them more agile, not only through the purchasing department, but also in other departments such as the technical office or project management. Here technology played a great role, with all the new digital tools for internal organization and even communication, they helped to create a link between the technical office and the purchasing department, avoiding possible communication failures, errors during the management of parts manufacturing and/or errors in the purchasing process. And also to eliminate unnecessary intermediaries and bottlenecks throughout the manufacturing process of the single-dose packaging machine.
With these actions we can clearly see INVpack's goal to innovate and improve. And for this, sometimes it is not necessary to make big changes, but it is important to prioritize, reorganize and modify certain ways of working and organizing internally. This is the only way to achieve INVpack's main objective: to offer fully customized vertical packaging solutions for each customer.
INVpack is gearing up for an exciting last quarter of 2023, filled with opportunities to connect...
2022 started with many expectations for business activity and interaction between companies after...
September 2023 brings a new event to get a first-hand look at INVpack's packaging and dosing...